Anti-bandit (hammer & axe glass)
Security glazing is either an all-glass construct, or a glass & polycarbonate composite designed to withstand measurable, complex loads from deliberate and sustained attacks. It is often the first line of defence to protect high value goods and property, areas, interiors and individuals, or to prevent escape or self-harm in a secure institution. In terms of the composition of materials used in this product, we classify two different types.All-glass construction consists of two or more layers of glass bonded together with a glass lamination interlayer. Although the glass itself will crack and break when attacked, it will remain in place, thanks to the interlayers. This type of glass has a limited level of security though and can only repel manual attacks up to a certain levelBS EN 356 provides test methods and classification for resistance of glazing against manual attack. The hard body drop test using a 4.11kg steel sphere to represent a blunt instrument, such as a hammer attack. To pass the test, the ball must not penetrate the glass.

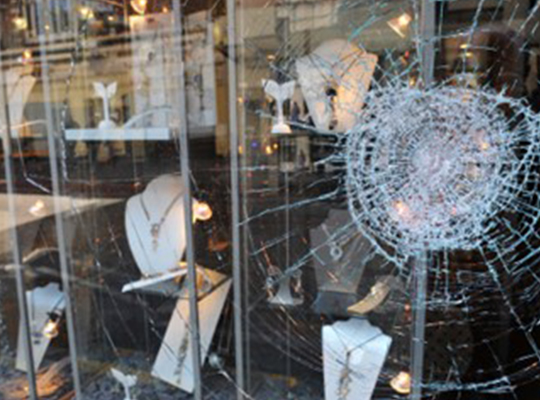
All-glass construction consists of two or more layers of glass bonded together with a ‘PVB’ interlayer. (Polyvinyl Butyral). Although the glass itself will crack and break when attacked, it will remain in place, thanks to the PVB interlayers. This type of glass has a limited level of security though and can only repel manual attacks up to a certain level.
BS EN 356 provides test methods and classification for resistance of glazing against manual attack. The hard body drop test using a 4.11kg steel sphere to represent a blunt instrument, such as a hammer attack. To pass the test, the ball must not penetrate the glass.
Testing Methods:
EN 356: 1999 Classifications
1. Hard body drop test
4.11 kg steel sphere (100mm diameter)
Glass resistance classes P6B to P8B are determined by the amount of hits executed by an axe in a controlled testing mechanism to create an opening for entry. The main purpose of these solutions is to protect interiors against vandalism, or delay/repel an attempted intrusion or extrusion long enough for the police or security services to arrive on the scene.
Bulletproof Glass
As mentioned above, the other security glass product is a composite of multiple layered, laminated sheets of glass and polycarbonate. The polycarbonate is situated either within the layers of glass or as a rear surface particularly in ballistic applications to achieve No-Spall properties. All-glass & No-spall products require a much thicker construct, making them significantly heavier. In terms of the direction of force, we distinguish an attack and a defense side. As the name implies the attack side is where the applied force gets in contact with the protective glazing. It is important to identify the correct direction as the construction of the sheets is usually non-symmetrical, so it is vital they are installed with the correct side facing the potential threat.
As residual damage is caused by impact pressure or shock, shards of glass can break away from the surface of the protection side, potentially causing serious injuries such as loss of vision or even death. Security glass with no protection against this secondary threat is called `Spall` (S) glass. `No-Spall` (NS) security glass must have a polycarbonate layer laminated to the whole construct as a `backing`, or appropriate numbers of glass layers to achieve the same. Being the last line of defense, the polycarbonate layer prevents the glass debris from escaping the construct. Based on the level of projectile protection (different calibers of guns), multiple layers of polycarbonate can be incorporated within the structure.
Infallible security with an uncompromised style
Consistent Flatness
Our advanced formulation assembled by our highly trained technical staff allows us to manufacture quality flat security glass. Where most asymmetrical glass structures are bowed during production, we are able to offer a consistent quality of flat glass without sacrificing Infallible security with an uncompromised style
Improved Transparency
Our formulas and manufacturing methods are made with the consideration of maintaining minimalistic features (e.g. weight, thickness...) This puts our security range among the lighter and most transparent products available in the market.
Security and much more
Our security range is designed, tested, and certified to provide maximum application diversity. We are able to combine and incorporate Fire Resistance, Switchable, Printer and Design, hygiene, and many other specifications in a single product...
Make the right choice
Glass Technique Technical Team is especially and continuously trained to engage designers engineers, architects, and project owners in order to design and
specify the most appropriate product for the right project.
There is a European test standard (BS EN 1063) for bullet resistant glass (BRG). However, BRG will need to be mounted in a window frame which should also be subject to testing in accordance with the separate, complementary standards for bullet resistant windows, doors, shutters, and blinds (BS EN 1522 and BS EN 1523).
When a bullet hits BRG, the glass is badly cracked for some distance from the point of impact. This means that a subsequent bullet may hit the glass that has already been damaged and weakened. To ensure this effect is assessed, the standard requires that three shots are fired so that the points of impact form a 120mm triangle. This ensures that any reduction in performance after the first shot is assessed.
The penetration of bullets is dependent on many factors, however, when it comes to firearms there are four main aspects to consider, such as type of firearm, caliber, velocity, and bullet type.
As there is an endless range of firearms available on the market, designers and manufacturers selected a limited scope of it for use in the standards for bullet-resistant products. These weapons represent the types of those that are likely to be used by terrorists or criminals and include handguns (revolvers, automatic pistols), military rifles, and shotguns.
The typical bullet velocities are:
Handguns 300 to 500 m/s
Rifles 700 to 1,000 m/s
Shotguns about 600 m/s
As mentioned above, the penetration of a bullet is dependent on both the weapon (which influences the velocity) and the ammunition being used. Most bullets are intended for use against people or animals and consist of a thin metal jacket (often of steel or a copper alloy) filled with a softer metal. Usually, this is lead but other alloys are now being used to meet environmental requirements. This type of ammunition is often called a “Ball” round. The highest threat level specified in the test standards is Armour Piercing (AP) bullets, which are designed for penetrating hard metals. AP bullets have hardened steel penetrating core inside a thin metal jacket. For the shotgun threat level, a single solid lead slug is used. This represents the concentration of lead shot that occurs at very close range to the shotgun before it has had time to spread.
The current British versions of European Standards 2 specify seven (plus one – BR4+ for Kalashnikov) threats using pistols and rifles, plus two threat levels using a shotgun. The pistols and rifles are listed in ascending order of threat severity.
The same threat levels are used in both the standards for bullet penetration performance (BS EN 1063) and the standard for glass and windows, doors, shutters, and blinds (BS EN 1522) with prefixes BR and FB respectively.
The standards also permit additional weapons to be specified if required. Although very widely available, the AK47 (Kalashnikov) rifle is not included in the standard threat list because of difficulty of defining test requirements as there is a wide variation in the performance of both weapons and bullets which are made by many manufacturers. The performance of AK47 bullets (7.62mm x 39) is generally worse than that of the equivalent NATO ball (BR/FB 6) or AP (BR/FB7).
Ballistic Steel
As previously mentioned, the frame is just as important as the glass when it comes to bulletproof and blast-resistant products. Ballistic steel (also known as armor or protection steel) is made of hardened martensitic steel that is used to protect against external threats. Martensite is a very hard form of steel crystalline structure with added carbon, a specific type of stainless-steel alloy, that can be hardened and tempered through multiple ways of aging/heat treatment. To harden this material, a heat and chill process is required, enabling this heat-treated and highly hardened protection steel plate to have excellent wear resistance against different scenarios. This ballistic steel withstands the high impact of stress and it is a tough, bendable, long-lasting, and weldable product with a wide range of applications. It is used within the defense industry and civilian applications to make cash-in-transit vehicles, vaults, bank counters, training facilities, security doors, police cars, and security booths.
Brinell Test
Ballistic steel is usually measured to 3 main criteria in order to achieve a bulletproof rating. These are hardness, yield strength, and tensile strength. There are several hardness tests like Brinell, Vickers, and Rockwell hardness tests, however, our industry predominantly refers to the first one.
The Brinell hardness is calculated using the following formula:
Brinell Hardness, HB = Applied test force in kilogram-force (kgf) ÷ Surface area of indentation (mm2)
This hardness test method makes the widest and deepest indentation of the existing test methods, allowing the test to be conducted over a larger surface area of the specimen. This provides test averages of hardness over a wider surface area of material, which has the advantage of taking into account surface and grain irregularities on the metal.
The sufficient HB for bulletproof steel frames is around 480-540 Brinell which equals to 1660-1880 MPa.
Yield Strength
The yield strength of stainless-steel measures the minimum force required to create a permanent deformation in the steel. Ballistic steel features a yield strength of 1000 MPa-1250 MPa.
Tensile Strength
The tensile strength relates to the point at which permanent deformation occurs when the material is pulled or stretched laterally along its length. Ballistic steel is around 1600 MPa.
Blast Resistant Glass (EN13541)
Blast-resistant glass is a similar composite product to bulletproof types. It combines the rigidity and compressive strength of glass with the plasticity and energy-absorbing properties of polymer interlayers, such as PVB. Resistance level classifications vary between `ER1` to `ER4 `depending on the corresponding amount of TNT, which is used in a controlled shock-tube test mechanism, to simulate a real-life explosion that can penetrate the glass by the shockwave and shrapnel. The glass should remain in the test frame and prevent glass debris from becoming a weapon by harming people on the protection side. The shock wave of an explosion can transform standard glass into deadly projectiles. Designed to be flexible, blast-resistant glass remains in its tested frame by absorbing the force of blast waves according to the respective blast resistance classification.
TechnoPACT is the registered Safety and Security brand. This product range focuses on security aspects of the glass where enhanced performance is required. Our team is eager to engage engineers, architects, and specifiers to provide the latest product development updates with all the possibilities. Technopact can be manufactured with Fire Resistant Glass, Switchable Smart Glass, or even incorporate design features such as digital print or fabric and mesh laminates to provide a unique aesthetically pleasing security solution.